Interview with Ryan Scott, Vapor Audio
A relatively new entrant in the speaker market is Vapor Audio. Their products are notable for the use of top-quality drivers and an extremely solid cabinet construction method using laminated Baltic Birch ply. As a direct-sales manufacturer, their pricing also suggests outstanding value. I asked Ryan Scott, the designer and principal, if he would share his insights and experiences on the path to becoming a speaker manufacturer.
JR: Hi Ryan, thanks for speaking with Hifi Zine. Could I start with the name – why “Vapor”? The speaker model names also reflect an interest in things meteorological. Are you a meteorologist by training?
RS: Yes, I remember as a kid growing up I’d watch storms roll into SW Missouri, just fascinated. I’d wait until the lightning was so close that I started getting scared before I’d head indoors. I always knew I wanted to learn more about the weather and severe storms. So I attended the University of Missouri and earned a degree in Atmospheric Science. The weather is still a passion of mine, and I get to show it in a somewhat geeky way through the names of our speakers.
JR: What triggered your interest in hifi? And how did you get started with building speakers?
RS: Honestly, I think it’s genetic. Both my parents have a passion for music, maybe it was their influence more than genetics, but either way it was predisposed. My father had this band, he played guitar and sang, sometimes good but usually pretty bad with both. But still, they had their moments. He probably doesn’t realize it, but watching him and his friends just rock out and have so much fun, keeping the three of us kids up until the wee hours of the morning, it was pretty cool.
So I had a foundation of music appreciation. I got into car stereo in High School, and naturally progressed into home setups once I had a house. I’ve always been handy with tools, and not afraid to bite off more than I can chew with projects… in addition to a bit of a cheapskate. So once I realized I wanted better speakers than I could afford, the obvious answer was to build them myself. It really started just that simply – realizing that if somebody else can build them, why can’t I?
What really got the ball rolling was building an AV-3 kit from Danny Richie at GR Research. Once I heard those for the first time it really lit a fire. I had to build more, and better. Pretty soon after I realized that what I was building had some magic of its own.
JR: As I recall, the Cirrus, which is still the center of your lineup as the Cirrus Black, was the first speaker that you designed and made with the stacked-ply construction method. Can you tell us how you came up with the initial idea for that design and how it evolved ?
RS: It’s really simple: if I was going to do it, I was going to build the absolute best enclosure I knew how. Doing the stacked-ply method gives you options that you just don’t have with regular wall construction. I can vary wall thickness as I see fit, even cut a void into the walls that I can fill. I could incorporate a 3″ roundover into the front to eliminate edge diffraction, I could shape the inside to minimize reflection back through the cone, etc. And I could make it look really unique as well. Plus, Baltic Birch ply is an excellent material, with the best strength-to-weight ratio of any wood product.
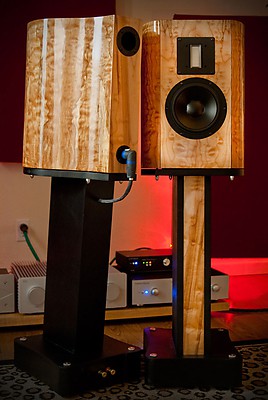
Vapor Audio Cirrus in crimson quilted maple, with matching stands
JR: Your website mentions the use of Finite Element Analysis to design the cabinets. What does that mean exactly?
RS: Finite Element Analysis or FEA is essentially just a computer simulation. These days it’s used to model anything you can imagine – jet engines, hard drive bearings, how a car will perform in a crash. They can be extremely complex, or relatively simple in scope. In our case, we used it to model the back wave off the woofer and how it would propagate inside the cabinet. The goal was to have as little as possible back-wave reflection into and through the woofer cone. We wanted all the sound inside to stay inside. Any of this “inside cabinet” sound that does get into the room will do so as pure distortion components, and in a near-time window that causes loss of soundstage focus.
As a result of the FEA program shaping the inside of our cabinets, we’re able to use about 1/4 the amount of cabinet stuffing typical for cabinets of the same volume. The FEA program also told us how much stuffing to use, and where, in order to eliminate the back-wave inside the cabinet.
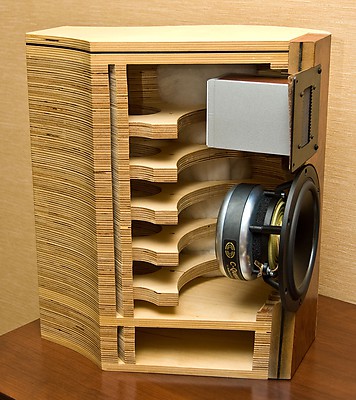
Cutaway showing cabinet construction of the Vapor Audio Cirrus
JR: I imagine that making the stacked-ply cabinets must be very labor-intensive! Could you walk us through the production steps?
RS: Haha, you could say that. I often regret the decision to do stacked-ply cabinets, usually after an hours-long block sanding session. First off, it took probably 10 pairs of cabinets before I finally figured out how to keep everything lined up when stacking. People assume every piece that comes off the CNC machine is identical – they aren’t. The sheet of plywood will move around slightly on the table as a bit is pushed through the wood, even when the board has been bolted down and is on a vacuum clamp table. As a result of things moving, they’re all off just a hair here or there. So when you stack, you focus on the areas that must stay aligned, and figure you’ll fix the others after it’s assembled. “Fix” means sanding, and because I made them so curvy, you can’t use a power sander for most of the work… it has to be done by hand with a block. Add to it that you’re sanding end-grain of hardwood, and you end up with some pretty sore forearms. If you’re doing a bare ply finish cabinet, it has to be sanded to 320 grit.
Once you get a totally square and smooth cabinet it has to be stabilized because the layers want to move over time. We seal the cabinets completely inside and out with marine epoxy, then sand the outside again. But even after your best efforts the cabinets end up just a hair off square, like half a degree left or right tilt, so the front baffles have to be cut by hand to match each cabinet. Even the plywood itself varies – some sheets are 17.9 mm thick, some are 18.1 mm thick. So when you stack up a cabinet made of 27 slices, the total height can vary by as much as 1/4″, which then has to be ‘shimmed’ to make them equal height.
When it comes to the veneer and finishing work, there’s been a lot of learning how to deal with problems. Real wood is finicky, and it doesn’t always co-operate. I wasn’t fortunate enough to have anyone teach me veneer or finishing, I had to learn it all on my own which means lots and lots of mistakes, until you figure out how not to make mistakes anymore. I’m probably doing a lot of things in a way that would make more experienced guys roll their eyes, but it works. I’ll tell anybody out there wanting to do veneer work of their own: get a vacuum bagger! Having that made my failure rate go to near zero, and opened up possibilities that just weren’t there without it. Look at the Cirrus – how would you veneer a curved cabinet like that without a bagger?
The production process consists of stacking, gluing and clamping, sanding, fixing problems, sanding some more, finding more problems to fix, sanding more, and then sanding some more for good measure! A conservative estimate is 100 hours in a pair of Cirrus.
A couple of things I tell people a lot: building a great-sounding speaker is easy, building a great-looking speaker is hard work. And that I’m proof that anybody can build nice-looking stuff!
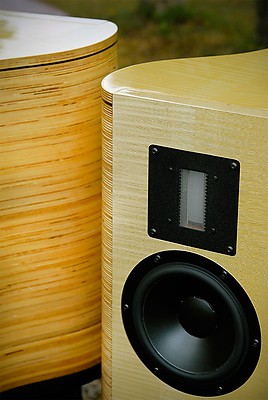
Vapor Audio Cirrus in flame maple finish with bare ply sides
JR: So, what possessed you to make the transition to speaker manufacturer? Did you have that already in mind when designing and making the first Cirrus, or did that come later?
RS: Good question… not being afraid to fail, I guess. I’ve been self-employed for almost 10 years now. I created some websites and sold them, published my own print magazine called RX Tuner for 3 years, was a full-time day trader, and a professional motorsports photographer. So once I realized I was creating speakers that were better than what was on the market, it just made sense to make a business out of it.
I did have it in mind when I started the Cirrus development process. And during the process I really began to question whether I was making the right decision or not. I had spent quite a large sum of money just to develop the first pair, and hadn’t sold a thing. But the people I trust urged me to keep moving forward and see where things go, so I did.
JR: I imagine that must be quite a change – to go from making a speaker to please yourself as a DIYer, to making speakers to please others as a manufacturer. What has been the biggest challenge for you in that journey?
RS: Easy: keeping organized. There’s no deadlines when building for yourself, and it’s pretty easy to keep yourself updated on progress. Keeping track of my inventory is always a challenge. Nothing is more frustrating than being in the middle of a step and realizing you can’t finish because you’re out of screws or wire that you need. When it comes to the work that’s done in the shop I always feel like that’s under control. But where I fall short at times is answering email, returning voicemail, keeping on suppliers to get product in time, etc. Part of that is spreading myself too thin, but we’ve made huge improvements in those areas and hopefully will continue to do so.
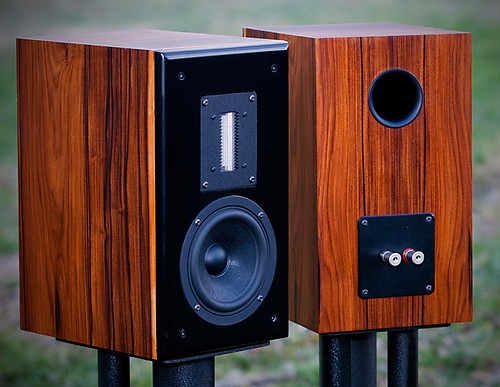
Vapor Audio Breeze in semi-gloss Santos rosewood
JR: Let’s talk more about some of the design elements of your speakers. The RAAL ribbon tweeter is clearly an important part of the Vapor sound, as it appears in most of the models. What distinguishes this tweeter from others that you considered, both in terms of technical specifications and its sound?
RS: Hobbyists I think focus too much on Frequency Response and Distortion. When you measure a RAAL there’s nothing in those areas to distinguish it from the other top tweeters available. It’s not until you measure its time domain performance that you see clear superiority – energy storage and rise/settle time is far better than the closest competitors. And when you think about a complex music waveform, it makes sense that the ability to stop and start quickly with no overhang is critical to reproducing that signal faithfully.
When you listen to one, you’ll notice that things just sound more like they should – more real. That speed allows it to clearly convey all the complexity in vocals and instruments, and all the layers of harmonics are clearly audible. The difference between a RAAL and a top dome tweeter is similar to that between a Redbook CD and a 24/192 recording. The common conception is that a speaker with more detail is more fatiguing, but the high-res recording isn’t more fatiguing, actually quite the opposite. The detail from a RAAL is like that of the high-res recording, it makes listening for long periods easier. High-res recordings just have this sense of ease to them, and that’s the same sensation the RAAL gives.
JR: The Arcus and Aurora are the two exceptions to the rule, each using a waveguide with an AMT (air motion transformer) and ceramic dome respectively. Could you tell us more about the design choices for these speakers?
RS: Both of those designs were determined by design goals. With the Arcus we wanted high sensitivity, high SPL capability, high resolution, and balance with all music – which most higher-sensitivity designs don’t give. After looking at all available choices, the Acoustic Elegance 10″ woofer was without a doubt the best fit. But to cross a RAAL to a 10″ woofer would require a relative low crossover point, which would compromise power handling. The very large element of the Beyma AMT makes possible a 1000 Hz crossover point, but still with a continuous 500 watts rated power handling. Being a form of a ribbon it’s also very fast and resolving. So we ended up with a stand-mount that can do 122 dB down to 50 Hz and still sound amazing at 70 dB. It’s probably the most versatile speaker in our lineup in that it does Home Theater as well as 2-channel Audiophile setups. You can use it with 8 watts, or 800. And it’s not the size of a Frigidaire.
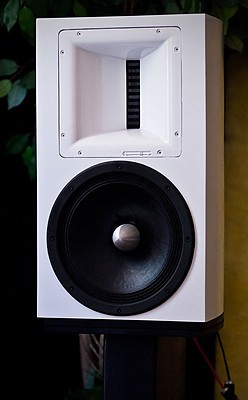
Vapor Audio Arcus, finished in Steinway Piano White
With the Aurora we wanted a near full range monitor – that means a woofer larger than 7″. But a woofer larger than 7″ means crossover points of 1500 Hz or lower. Those low crossover points make the RAAL a poor fit. At RMAF 2007, I showed a speaker that used a large 10″ waveguide with a ScanSpeak AirCirc tweeter. That tweeter was crossed over at 875 Hz, and never showed strain at all. So based on that experience we began developing some new waveguide profiles. We had 6 different profiles printed on a rapid prototyping machine and then tested to see what gain profile and dispersion pattern they produce. After we settled on the best, we began searching for the best dome tweeter to match with it, which was a challenge – once you get used to the RAAL, the vast majority of dome tweeters just sound boring. And for over a year we used tweeters in the Aurora that just didn’t excite, until we found out about Transducer Lab. They produce tweeters by hand in the USA without compromise – similar to what we do. Their domes have low moving mass and extremely high motor force, along with rigid pure ceramic domes. They’re the best dome tweeters I’ve heard, and I’m quite happy that we found out about them.
JR: Is the waveguide advantageous if the listening environment is only lightly treated acoustically?
RS: A lot of times there’s a disconnect between the theoretical world and the real world. The internet pundits will tell you that controlling the directivity makes room interactions less severe, and makes placement easier. Compared to our RAAL-based designs, that just hasn’t been the case – the wave-guided speakers are actually more finicky with respect to room placement.
In my experience with waveguides, the benefit isn’t controlled directivity; I haven’t ever heard anything that made me say “wow, listen how controlled that dispersion pattern is!” There’s no controlled-dispersion sound that I can hear. The benefit the waveguides do provide is gain on the low end of the tweeter, which, when EQ’d back to flat in the crossover, results in lower distortion and less load on the tweeter. That can make the tweeter sound more dynamic and able to produce more output before showing strain. It also allows a lower crossover point. Those are all real effects you can apply to meet design goals.
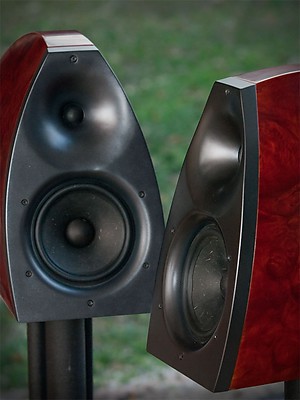
Vapor Audio Aurora in Pelin Burl buffed satin
JR: I gather that in general you prefer simpler crossovers with high-quality components. Can you tell us more about how you arrive at your choice of crossover components and topology?
RS: I prefer as simple a crossover as the drivers will allow. And more often than not, drivers that allow simpler crossovers sound better. We let the drivers tell us what they want, not try to force them into our ideas of what’s right. We extensively voice everything we design, and I trust my ears more than I trust the microphone. Shallow slope networks do often give a sense of refinement, or smooth sound… but only if the chosen drivers allow. Shallow slopes can also give a more enveloping holographic soundstage than steeper slopes, at least for the drivers we use.
I don’t want to speak in absolute terms, because the situation can be different for every design. Some designs will want steeper slopes for best sound, but typically that means one of the drivers has a problem area that needs to be hammered down into inaudibility. When you find drivers that sound best with shallow slopes, that means they’re well-behaved far outside of their passband. I think any designer would agree that’s a good thing.
So, unlike some other designers, we don’t have topologies we stick with, we use whatever works best given the design. And we let our ears decide.
That reminds me of another huge key to success: trusting your ears. Your ears can be trained, and you can learn critical listening. I thank Chris Hoff of Balanced Power Technologies for helping me learn the art of critical listening, he has an excellent ear and was a sort of mentor for me along the way. If he reads that he’ll probably blush. But critical listening is focusing on the micro, not the macro. Where exactly is that trumpet in space, is it stable in its location or does it move as the notes change? Focusing on the small things like that will tell you if you’ve found success, or if there’s more work to be done.
JR: I expect it’s hard to describe, but how audible are the differences between the various crossover upgrade options that you offer? How would someone know which one to choose?
RS: It depends on the listener among other things. I can hear differences clearly every time, but some people I know who come here often and listen to in-progress designs have more trouble picking out the differences. One of my co-workers also has high acuity to these differences, and we challenge ourselves with listening and not telling each other impressions until finished… and then comparing notes. When your impressions are identical, you know you’re not just making things up. That said, the upgrades offer subtle changes. Even the mighty Dueland CAST capacitor isn’t a revolutionary change from our standard configurations. But it’s that last 5% that people are often willing to pay for, and that’s where the upgrades come into play.
Most customers don’t come to me saying I want Brand X capacitors, and Brand Y wire. Most ask what my impressions of the differences are, and that’s the right place to start. I don’t want to be a used car salesman pitching the $500 clear coat protectant because that’s where my margins are. I don’t mark up my upgrades. The hope is to give the customer the sound they want, and when you have a very neutral and resolving speaker to being with, things like changing capacitors can “flavor” the sound to suit the customer’s taste. For instance, if in talking with a customer they say they like a more musical and romantic presentation, I’ll recommend the Jensen copper foil/oil caps. If they want the ultimate in clarity and imaging I’ll suggest Dueland CAST. I probably spend as much time talking capacitors with customers as any other element of the build.
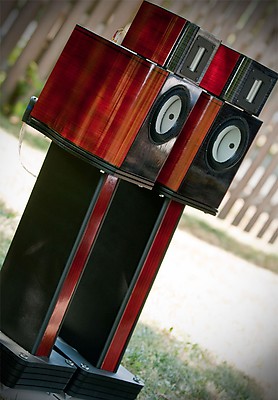
Vapor Audio Cirrus White with matching stands
JR: I note with interest that the Cirrus White is specifically designed to be used with a subwoofer. What is your take on a no-compromises solution here? Have you thought about producing a sub yourself?
RS: I love open baffle bass, it just has a natural sound that integrates better from my experience. So my ultimate solution is many large drivers (15″ or 18″) in some form of open baffle configuration, tons of power, and proper EQ to bring them all to flat at the listening position. But that’s a hard solution to package and sell to a customer. It’s certainly not a turn-key solution. I do want to produce subwoofers at some point, and when I do, it will be along those lines. The technology exists at price points to make it possible, and package-able into one central brain and amplification box.
I can see a solution where the customer receives either 2 or 4 OB subwoofers, something like a slot-loaded W-frame. And then also receives a box with 2 or 4 channels of amplification and a calibration mic to plug into it. Push a button and it sweeps through the subs, calibrating each one individually. Add to that a Bluetooth interface so one could tweak it with software on your smartphone, and then you’d really have something! We’re working on it.
JR: To close, let’s get back to why we do all this! What are your favorite artists or albums at present?
RS: I don’t listen to typical audiophile fare. I grew up on Metallica, Megadeth, Anthrax, Motley Crue. Of course I listen to audiophile recordings during voicing, but once the voicing sessions are over I put on Nine Inch Nails or Tool. My father greatly admires Bob Dylan for his insight and creativity – I often tell him that Trent Reznor and James Maynard Keynan are the Bob Dylans of my generation. I listen to music for the emotion, and hard edgy music gives that to me. I still listen to a lot of Megadeth, and think Rust in Peace is one of the greatest albums of all time. I also listen to a lot of Electronica, another album on my all-time list is Paul Oakenfold’s Tranceport… too bad it’s a horrible recording. Lately, dubstep like Skrillex and Infected Mushroom has been getting a lot of play time around here as well.
For a long time my goal was 10,000 albums on my music server. I passed that and now have around 22,000. I do honestly love music of all types, as long as it’s real and has emotion. Recently a friend of mine has introduced me to quite a few new favorites like Anouar Brahem, Nik Bartsch, Yello, Rome, and Coil. That’s some pretty off-the-wall stuff, but it has great emotion.
The most exciting music news I’ve received in some time was Trent Reznor recently announcing that Nine Inch Nails would be doing some new studio work. I can hardly wait!
JR: Thank you Ryan, all the best at the upcoming Axpona show and in the future.
RS: It was my pleasure John, thank you for letting me speak to your audience. It was an honor just being considered.
Exquisite workmanship on the Cirris, Ryan. Beautiful, too I love the banded sides of the cabinets. Thanks for the article, John.
Good to see you enjoyed my idea of a laminated speaker design. I first came up with this idea 20+ years ago and filed the initial patents in the UK but never followed the idea through.